This article was originally published on Manufacturing Dive.
Automating manufacturing processes is a crucial goal of many digital transformation projects. The transition to digital initiatives helps manufacturers achieve operational efficiency, resiliency, and sustainability.
For many factories, automation relies on Industrial Internet of Things (IIoT) technology to enable everything from system controls and asset tracking to predictive maintenance and autonomous robots. The foundation supporting IIoT technologies is resilient networks—on-premises or cloud-based—that facilitate robust data collection, artificial intelligence (AI) and machine learning (ML), and apply predictive analytics to keep the entire infrastructure adaptable and sustainable.
IT plays a critical role in helping manufacturing organizations scale by using data-driven manufacturing to enhance productivity, thereby accelerating Industry 4.0 projects using automation to enhance the workforce and automating operational technology to increase safety and security.
Data-driven manufacturing increases productivity
To keep up with the rapid pace of change in manufacturing, IT leaders need deeper visibility into the network and thousands of connected endpoints. By continuously collecting data from manufacturing floor sensors and IIoT devices, IT can help track what is happening NOW and provide dashboards for plant managers and engineers so they can identify trends, predict outcomes, and detect potential problems before they affect production.
IT must also address how a manufacturing organization can efficiently scale to encompass new products, services, and customers. Automating network management is essential to enabling IT to rapidly change network configurations, add security policies, and extend connectivity to new locations. For example, when demand for certain goods increases dramatically—as was the case for medical equipment and supplies during the pandemic—the processes already in place must quickly scale to produce new products or modify existing ones. That can mean adding new warehouses, expanding factory floor lines, and reconfiguring supply chains. To support these changes, IT needs the ability to scale by expanding wireless connectivity to new locations, onboarding thousands of different device types, and integrating new partners into the supply chain.
Industry 4.0 poses ongoing challenges for IT
Manufacturing IT teams face ongoing challenges as organizations embark on Industry 4.0 initiatives to digitalize the existing infrastructure to adapt to new products and markets dynamically. To embark on the Industry 4.0 journey, IT needs to connect distributed computing resources at scale so the workforce can access applications from wherever they are to monitor and control operations in real time. In addition, IT needs to support the ability to collect data from sensors added to existing equipment on the plant floor and to remote edge locations.
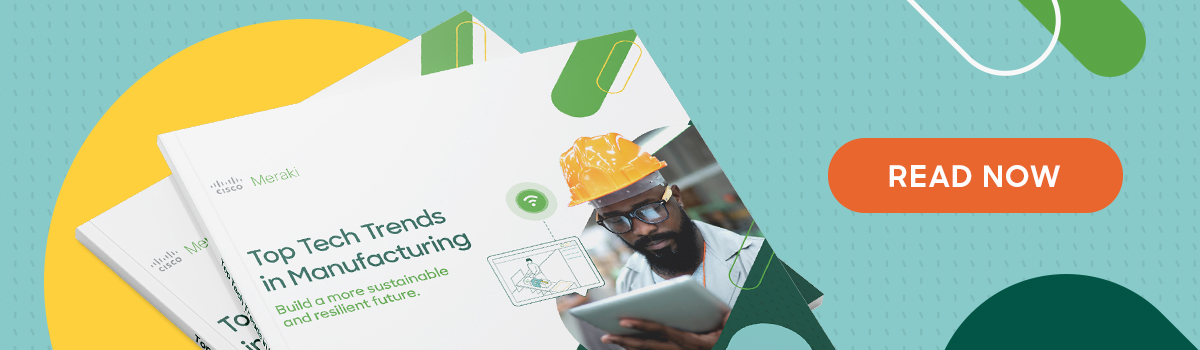
But managing these distributed computing resources and providing secure connectivity adds a layer of complexity to IT operations. To simplify the complex, IT can apply AI and ML tools to monitor computing resource usage and balance network traffic loads by dynamically choosing the most efficient routes. AI/ML systems can automate troubleshooting with predictive alerts that warn of abnormal behaviors before they can affect production.
Augmenting the workforce for productivity and retention
With all the technology woven throughout manufacturing processes, it’s critical to keep human-centric consideration at the forefront of planning for automation and scale. Recent economic challenges coupled with a steadily retiring workforce have led to staffing shortages and the loss of skill sets. Automating processes to minimize manual repetitive tasks enables people to concentrate on mentoring the incoming workforce and focus on more creative work tasks to keep them engaged and learning.
Another way to combat repetitive labor processes in some manufacturing roles is to employ robotics to perform tasks such as delivering materials from the warehouse, safely manipulating massive loads, and working in hazardous environments. Cobots, or collaborative robots, are increasingly used to supplement human labor, taking on the repetitive strain of assembly processes and freeing human ingenuity on production lines to improve quality outcomes. These semi-autonomous robots require ultra-low latency networks to function safely and adapt to the environment around them. IT must ensure reliable connectivity so robotic systems can perform 24×7 as production schedules require. Robotics in either form elevate efficiency while making the workforce safer and more productive.
Automate operational technology for safety and security
Building on the safety that automated robotics can bring into the factory, networked smart cameras and motion sensors enable operational technology (OT) managers to monitor security, environmental changes, and personnel safety throughout warehouses, plant floors, and data centers from a central location. By adding a layer of ML to analyze the data streaming from these devices, humans don’t need to continuously monitor every location because they are alerted only when predefined anomalies occur. Combined with sensors for temperature, water leaks, and humidity levels, vast areas of a manufacturing facility can be monitored 24×7 to minimize interruptions to operations by accidents, security breaches, or environmental impacts.
Network automation: a recipe for success
As manufacturing organizations scale processes to adapt to market changes, new products, and customer requirements, so must the networks that tie every device, application, and person together over distributed organizations and hybrid workforces to match the needs of the enterprise. Automating technology and processes enables IT to adapt to and manage complex industrial networks. Working toward automating everything prepares the manufacturing enterprise for growth and success. Learn how a cloud-managed platform that converges IT, IoT, and physical manufacturing environments can unlock countless possibilities.